Sugar Plant & Spares
BI-Drum, Multifuel Industrial Boilers
Main Features
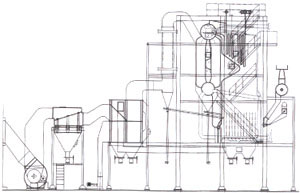
- Suitable for indoor & outdoor application.
- Top supported units allowing free expansion at the bottom.
- Multi-fuel application.
- Provision of reliable fulr feeding, controling, distributing system.
- Chevron drier with horizontal steam seperator for high steam quality.
- Attemperator with controls for maintaining constant superheat temperature over wide range.
- Furnace with membranewall construction (wherever required).
- Safety interlock & advanced system of boiler instrumentation & control for safe operation, monitoring & achieving higher efficiency.
- Microprocessor based systems, PLC, DCS, SCADA incorporated wherever required.
- Easy access for each part.
- High combution volume ensuring complete combution.
- Tall combution chember.
- Large grate area.
- Automatic draft control.
Application
These boilers are suitable for burning of either individual or in combination the fuels like coal, oil, gas, rice husk, bagasse, biomass and other agricultural wastes.
Coal firing units may require continuous ash discharge traveling grate, where ash percentage is high. The coal with small ash percentage and other solid fuels are successfully burnt on dumping grate.
Furnace Dimensions
Conservative rates of heat release, both for combustion chamber and grate are selected for all fuels. Grate dimensioning of furnace and arrangement of further heating surfaces such as super heater, convention bank, economizer and air heater run minimum risk of clogging, even in case of over loading. The soot blowers, retractable and rotary provided are sufficient to keep the surface clean for longer period which is a requirement for boilers for co-generation.
Symetrical Design
Box type combustion chamber uniform gas velocity. The bank tubes are evenly placed, as a result, gases leave the furnace at fairly uniform temperature. With the feature;
- Uniform evaporation across section.
- Uniform water level in the drum
- Uniform expansion of pressure parts is achieved. These features result in quick response to rapid load swing, carry high rating and produce dry steam at all loads.
Superheater
For reducing superheater tube metal temperature, the heating surface is divided in two section with counter flow and parallel flow arrangements. The attemperator, to control the steam temperature is, placed in interstage or at the outlet, depending on the final steam temperature requirement.
Large Air Heaters
Large Air Heaters are provided for higher heat recovery and therefore higher efficiency. The hot air assist combustion and makes furnace condition more suitable.
Over Fire Air System
To reduce smoke and fly ash, over fire air system is used. Over fire air burns vaporized volatile matter which is in high percentage in Bagasse.
Cinder Return System
These are offered where improvement in efficiency and operational ease is important, particularly for large size boilers.
Spreader Stroker
Spreaders strokers for coal are mechanical, where as for bagasse and similar fuels are pneumatic. These are designed for suspension burning of lighter particles and uniform distribution of fuel on the grate. Location of spreaders are so decided that with minimum carry over of lighter particles in suspension.